數控cnc五軸加工是一種精度高、高復雜度的加工技術,通過五個坐標軸(三個線性軸 X/Y/Z 和兩個旋轉軸 A/B/C)的聯動控制,實現對復雜曲面、多維度結構的精密加工。
?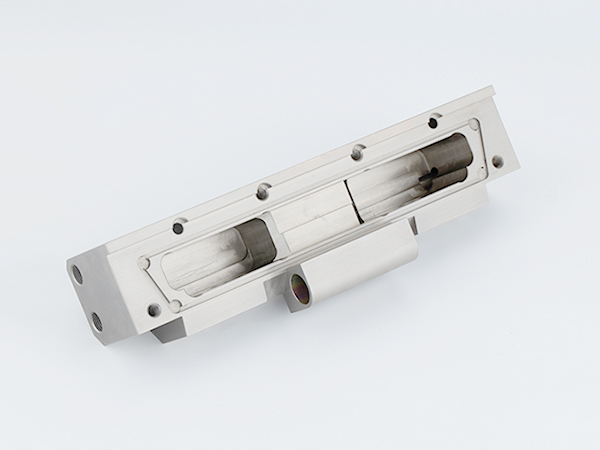
那么,關于其核心優勢與挑戰分別有哪些呢?
優勢:
復雜結構一次成型
減少裝夾次數(三軸加工需多次翻面裝夾,五軸可一次完成多面加工),避免重復定位誤差,提升精度。
案例:加工航空發動機整體葉盤時,五軸機床可直接從毛坯銑削出葉片和盤體的復雜連接結構,無需分段加工再拼接。
提升表面質量與效率
刀具可沿曲面法向傾斜切削(避免三軸加工中的 “側刃切削” 導致的紋路不均)表面粗糙度降低 50% 以上,減少后處理工序。
采用擺線銑削、螺旋插補等五軸專屬工藝,可高效加工深腔、窄縫等結構(如模具中的肋板、航空結構件的減重孔)。
降低材料與人工成本
減少工裝夾具數量(一次裝夾完成多工序)縮短編程時間(CAM 軟件自動生成五軸路徑)適合小批量定制化生產(如醫療器械個性化假體)。
挑戰:
設備與編程門檻高
五軸機床價格昂貴(通常為三軸機床的 3-5 倍)且維護成本高(需定期校準旋轉軸精度)。
編程需掌握復雜的坐標變換(如刀具長度補償、旋轉軸半徑補償)需使用專業 CAM 軟件(如 UG NX、PowerMill、Mastercam),對工程師經驗要求高。
加工工藝復雜
刀具姿態控制難度大(如刀具與工件干涉風險)需通過仿真軟件(如 VERICUT)提前驗證路徑,避免撞刀。
切削參數優化復雜(如針對鈦合金材料,需平衡切削速度、進給量和刀具壽命)需大量工藝試驗積累。
精度與穩定性要求高
旋轉軸的定位精度(如 A 軸分度誤差≤5″)直接影響加工精度,需定期進行機床精度檢測(如激光干涉儀校準)。
大扭矩切削時(如加工合金鋼),機床剛性不足易導致振動,影響表面質量。